The proposal is structured to align within the Small Air Transport (SAT) transverse activity by proposing not only a conceptual design, but also a larger mobility context to include small aircraft in a multimodal passenger and freight network. The investment analysis provided in the scope of the project will offer ideas for the market revitalization of the European small aircraft industry. Considering the size of this 19-seater airframe and the foreseen technology advancements, this proposal also includes a CleanSky “Technology radar” task to scout developments in other ITD’s that can find application in the proposed concept, in the attempt to seed tomorrow’s UNIFIER19 supply chain.
Design framework
The aircraft concept to be developed is a NZE 19-seat airframe with multiple cabin layouts for passenger seating as well as cargo, powered by a modular hybrid-electric powertrain. To accommodate and successfully operate on the markets identified, different propellers and different combinations of battery and range-extending technologies will be tailored for each of the markets identified. Designing today a hybrid propulsion with modular solutions also allows that tomorrow this same aircraft will be easily upgradable with better performing systems via supplementary type-certificates to further extend its commercial life.
In order to achieve an aircraft configuration that meets the proposed objectives, the consortium will adopt a design strategy consisting in the activities grouped in the following paragraphs.
Community friendly miniliner: setting design requirements for a new mobility experience
Our design requirements start with providing to our citizens a new, near-zero emission travel experience. The design requirements include:
- Embarking/disembarking experience as easy as a bus: access provisions integrated in the airframe featuring facial recognition to authenticate pre-registered and security-approved travellers to permit pick-ups from runways with no ground infrastructure.
- Operations from unpaved runways: lowering the infrastructure investments from municipalities exponentially increases the number of communities served by this miniliner.
- propellers/impellers configured and actively controlled to have an acoustically acceptable spectral signature: to avoid the “not in my backyard” syndrome.
- Flexible cabin layout: passengers, cargo, mixed use or medevac to increase versatility.
- Fly-by-wire control system: to integrate propulsion response in the control laws, to increase cruise performance by reducing trim drag, to reduce pilot workload in the envisioned single-pilot operations and to facilitate future upgrades to autonomous/remotely-piloted flight.
The basic requirement to use unpaved runways, the reconfigurable cabin and an airframe suitable to be powered by different versions of the propulsion system without changing its structure represent outstanding technological aspect of the proposed project. In addition, another novel input is the mission itself, being more related with operational and socio-economic aspects. By using a demand-modelling tool under development by POLIMI in the EU H2020 project MAHEPA a light market study will be performed. The tool calculates the number of prospective passengers that may gain a significant time advantage if flying from rural airports to a city airport instead of driving, based on socioeconomics, population data, existing mobility infrastructure specifics, etc. From this market study, two market scenarios are expected to be identified. This shall point out the need of a modular propulsion system for the same airframe, tailoring the propellers, batteries and range-extending technologies for different climb/cruise/range performance profiles and shall determine whether there is a real need for a pressurized cabin. This light market study shall also provide crucial data about the target missions, in order to finalize the list of requirements for which the UNIFIER19 configuration shall be optimized in the quantitative design loop.
The systematic solutions space sweep with qualitative evaluations
Hybrid-electric propulsion is one of the enabling technologies for quieter, more efficient and environmentally sustainable aircraft. Lightweight electric motors can be structurally installed on the airframe, where beneficial airframe-to-propulsion interactions may be created. Their wide rpm range permits to design propellers and ducted fans which are quieter and more efficient than conventional designs. In a distributed propulsion configuration, the wing surface area can be minimized without sacrificing fundamental performance, such as take-off distance. Additionally, the effect of distributed propellers can be integrated in the fly-by-wire flight control architecture to augment the authority of aircraft control surfaces, resulting in overall system mass reduction.
These and other features translate into a very wide solution space, which is currently being explored in many research papers that often claim spectacular energy efficiency achievements, typically addressing simplified aircraft and operation models. In this proposal, one of the project’s strengths is the systematic approach devised to analyse this solution space and extract the optimal configurations, which not only cater for near-zero emission travel, but that can actually be built, certified and sustain commercially successful operations in the near future.
The approach devised is to initially explore a wide solution space of airframe/propulsion configurations (such as dedicated propellers for cruise and take-off, blown wing, wing-tip propellers, tail-mounted ducted fans, etc.) and propulsion system designs (such as high-energy-density liquid hydrogen-powered cells, hybrid power-energy batteries, high-torque multi-winding motors, SiC distributed inverters, etc.). Numerous configurations have been already analysed by POLIMI and TUDELFT in past and current research activities. This extensive know-how will be correlated with an in-depth literature review to ensure a systematic, comprehensive approach. Similarly, PVS engineering experience in developing and certifying electric propulsion systems currently marketed under Pipistrel’s brand will be integrated with the state-of-the art review of upcoming propulsion technologies.
These combined airframe-propulsion configurations and propulsion systems will be qualitatively rated by POLIMI and TUDELFT in terms of potential for chemical and noise emission reduction. The resulting scorecard will be completed by PVS according to its experience as a manufacturer, integrating knowledge on what can be built and certified using existing CS-23 or upcoming standards, in particular ASTMs where PVS participates as a standard development member.
The resulting qualitative rating represents a resource-efficient preparatory activity for the consequent design loop in which quantitative evaluation will be performed. It has also the advantage to allow a quick examination of a wide solution space, thus helping in finding a better result than by pitching and fixating on an aircraft configuration at the proposal stage.
The concurrent design loop with quantitative evaluation
The design loop itself requires highlighting the most promising configurations and sharing them between POLIMI and TUDELFT for an optimization using low- and medium-fidelity tools, with PVS providing analysis on propulsion architecture aspects with estimates of maintenance complexity and production costs to both academic partners. This conceptual design stage will consist of the integration of several disciplines that usually considered in aircraft design such as: preliminary aerodynamic analysis, weight estimation, architectural configuration and sizing of the propulsion system. In addition, partners will integrate preliminary models accounting for possible interaction effects. The metric used in the design loop will be a combination of an emission index and a success index, defined specifically for the purpose of the project. The emission index is a weighted indication of acoustic and gaseous (CO2 and NOx) emissions, while the success index combines estimates on development costs, certification costs, maintenance complexity and operating revenues on identified routes.
It is worth noting that this approach not only delivers an aircraft design which has low emissions, but has also a bankability aspect, which can be the exploitation enabler for the proposed solution. Additional considerations will be made for the case of hydrogen-powered propulsion: a fuel-cell powered aircraft is a zero-emission vehicle, but if the cheapest hydrogen is produced in an environmentally dirty process, those emissions will be factored in the final report.
The best configurations developed by POLIMI and TUDELFT will undergo a final re-evaluation using the one-stop shop in data methodology. The one-stop shop will require the academic partners to re-evaluate their best configuration using the same procedure, to ensure consistency in performance metrics. In fact, it has been observed in past cooperative projects that the same configuration can be benchmarked differently when tools developed independently are used.
The workflow can be visualized in the breakdown diagram shown in Figure 1.
Figure 1. The concurrent design loop workflow
The detailed evaluation of the winning design configuration
The winning configuration will undergo a high-fidelity synthesis according to a workshare between the partners for each subsystem and discipline (aerodynamics, structures, propulsion, flight control and systems), avoiding any concurrent activity, if not required for cross-check. PVS will be responsible for the systems and the propulsion architecture design including the propeller design, the FHA/FMEA and a more detailed estimate of certification complexity, certification costs, production and maintenance costs. POLIMI will take over weight and balance, structural sizing and basic aeroelasticity, as well as operational aspects including the sizing of ground infrastructures. POLIMI shall also contribute to performance, stability and control analysis. TUDELFT will use an extensive CFD simulation campaign in order to assess the aerodynamics characteristics under different operating conditions so that cruise and low speed characteristic can be determined. Those CFD analyses will be particularly oriented in establishing relation and quantifying effects of the interaction of the lifting surfaces with the propulsion trust devices. This last activity will result in a strict collaboration with the propeller design activities carried out by PVS. When possible and depending on the typology of the propulsion/airframe interactions, the CFD analysis will be calibrated/verified on the basis of previous experimental campaign conducted by TUDELFT.
The different design disciplines will be integrated through the determination of a common data exchange structure. This activity will prevent any possible slowdown in the design process due to lack or wrong communication between partners. In addition, the possibility to determine a common design framework where each partner becomes responsible of its own discipline management and TUDELFT plays the role of the “process architecture” will enable also the possibility to improve the design loops and iteration effectiveness during the synthesis of the configuration when using high fidelity tools as reported as example in the diagram of Figure 2.
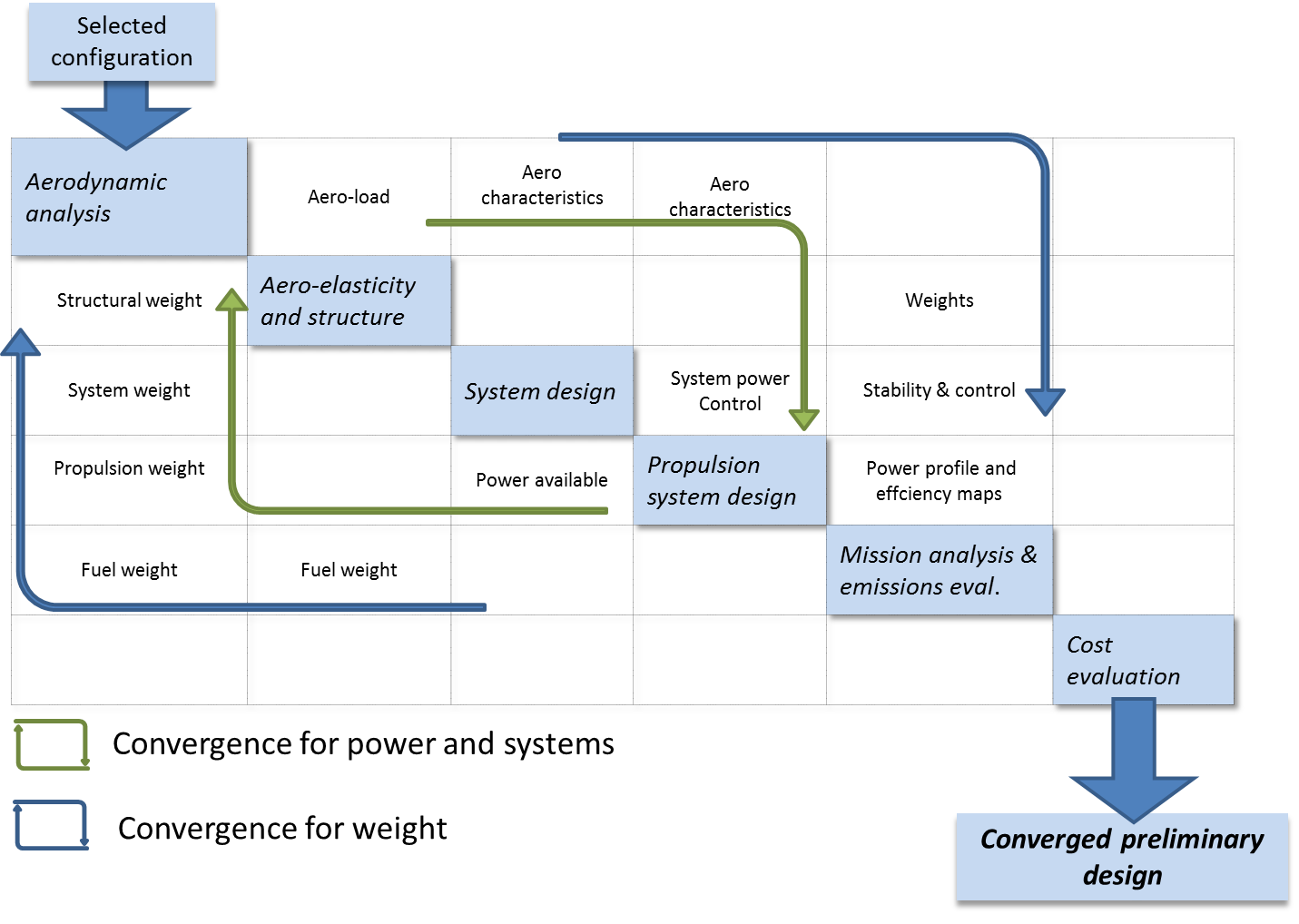
As reported in the diagram of Figure 2, where input/output data are only partially reported, multiple iterations are needed to achieve convergence of the configuration, remarking once more that an efficient data exchange environment can effectively improve the overall sizing, guaranteeing a faster and more reliable convergence.
The final configuration will undergo a high-level integration study on systems and propulsion to:
- evaluate possible synergies, such as utilizing internal and external structural members as cooling elements,
- ensure prevention on common mode failure propagation,
- secure electromagnetic compatibility/interference mitigations,
- include safety provisions as identified by the FHA/FMEA,
- estimate fuel and energy consumption by modelling different power management strategies at mission level,
- implement possible insulation strategies to prevent electric arcing.
The project will be rounded by a gap analysis and a roadmap study for performance critical technologies, plus an investment plan to chart the path from the conceptual design to in-service induction of the proposed UNIFIER19.